Special engineering
From construction to assembly and subsequent service, complex production machines / production lines are realized for our customers in special machine construction.
All work steps of the process can be carried out in-house. A high level of flexibility and short decision-making processes round off our strengths in this area.
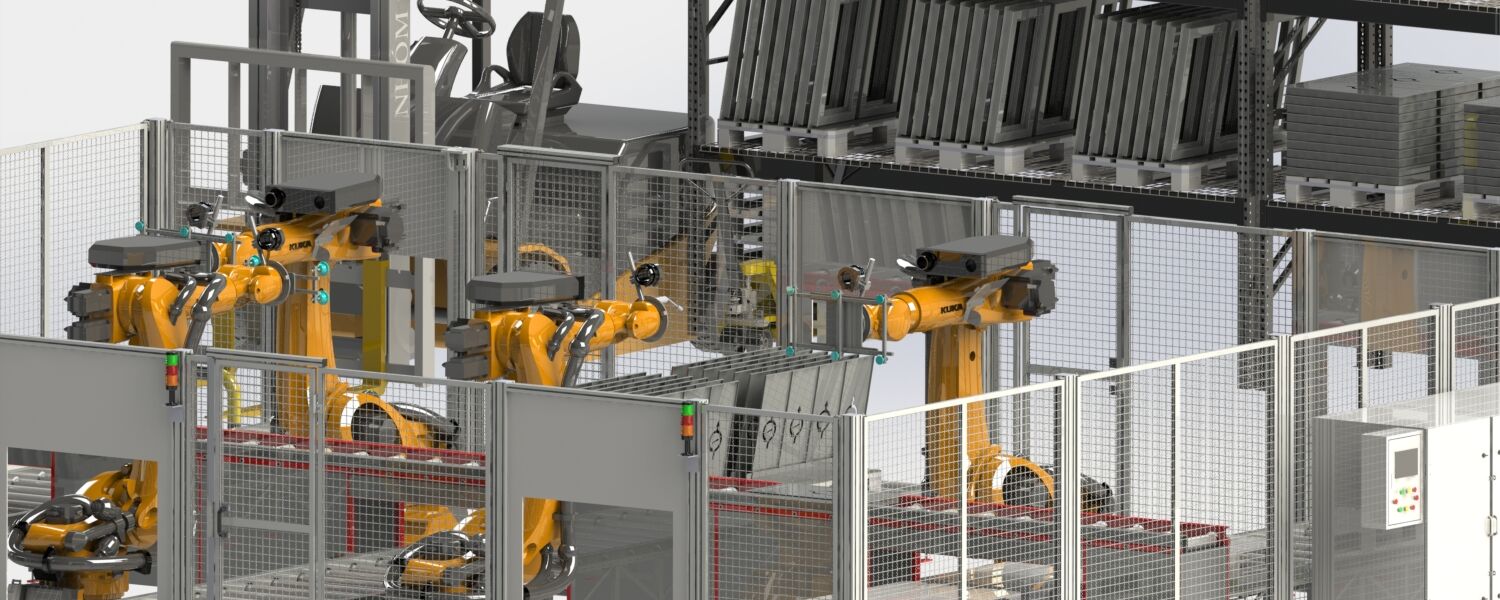
Drum turner for plate material - type TW600
Technical data:
Payload: | 500 kg |
Plate with: | 1.600mm |
Plate lenght: | 300mm |
Turning time: | 6 sec |
min/max speed: | 0,1 – 40m/min |
For turning panel material such as furniture, plastic panels, hard foam panels with surface treatment on both sides.
The components are held in position flat over hold-down devices during the turning process.
The goods can be conveyed in or out by roller or chain.
Several individual cuts (batches) can also be turned in one operation.
Large ring coil winder with automatic drum - type GRB 5000
Technical data:
Payload: | 5.000 kg |
max. winding width: | 2.400mm |
max. winding height: | 900mm |
min/max winding core: | 1,9m – 2,5m (stufenlos) |
min/max speed: | 0,1 – 10m/min |
Large coiler for winding plastic pipes with a diameter of up to ø200mm. The drum consists of 8 segments, which each consist of trusses. These trusses transfer the loads to the supporting star, so that no front support is necessary. The diameter of the drum can be infinitely adjusted, so that after the ring body has been produced, the core diameter can be reduced and the ring can be easily removed.
In addition, the entire system can be moved via a roller, which enables flexible use of the system on different lines.
Pallet turner PL15
Technical data:
Payload: | 1.500 kg |
Pallet width: | 2.850mm |
Clamping range: | 400- 2500mm |
Turning time: | 20sec |
Hydraulic drive |
For turning different goods on pallets. The system clamps and rotates via hydraulic drives. The tension is centered so that the mechanics are protected. The two clamps are synchronized via toothed belts. The PL15 pallet turner is extremely robust and impresses with minimal maintenance.
Alternatively, a ramp can be supplied. The feed area is secured by light barriers. Is secured on the side by means of a machine safety fence.